
CFD study eliminates downtime, improves efficiency for pet food manufacturer
To improve cooking time, a pet food manufacturer takes a look inside their oven — without taking it apart.
The client:
Using a proprietary steam manufacturing process, this confidential client supplies a rapidly growing market with premium-grade pet food.
To keep up with demand, they’re constantly looking for ways to increase throughput and drive efficiencies while protecting the quality that their consumers expect.
Project Details
Client
Confidential Client
The challenge:
This client theorized that small adjustments to their enclosed steam cooker ovens would drive big improvements in their cooking line’s overall efficiency.
The problem lay in the practicalities of investigating this notion. They would need to open up an oven, causing significant downtime without any guarantee of a result. Their theory was just that: a theory. Before taking action, they needed to know if, when, and how that action would pay off, and they needed to be certain that it wouldn’t impact product quality.
They started by working with their equipment vendor. The vendor adjusted a few variables without meaningfully impacting the cooking time. That’s when the vendor suggested that this client undertake an analysis of the equipment using computational fluid dynamics, or CFD. If an opportunity existed to re-engineer certain components inside the oven to improve cooking time and, as a result, expand throughput, CFD would find it.
What is CFD?
Complex though it may be in practice, a CFD model is simply a computational environment built to satisfy the three conservation laws of physics—that is, the conservation of mass, energy, and momentum.
Just as a basic calculator is “taught” the principles of arithmetic in order to deliver accurate sums, engineers can use these physical laws to teach a powerful processor how to accurately model fluid in motion within a simulated environment. Aerospace engineers were early adopters of this analytical method. They use CFD to model drag, lift, turbulence, and other dynamic variables, leading to safer vehicles for flight.
Today, CFD is used across many industries. Your weather app uses a CFD analysis of atmospheric and oceanic conditions to provide a daily forecast. The ventilation system in your building is probably based on a CFD analysis of optimal airflow. Even your electric kettle may have a CFD origin story—mechanical engineers likely used CFD to perfect its thermal performance.
The big draw of CFD is that it allows engineers to run scenarios, measure risk sensitivities, and pressure-test hypotheses before investing in real-world solutions.
How is CFD used in food manufacturing?
In a food manufacturing environment like the one in which this client operates, CFD means:
- Sustained product quality: Engineers can use CFD to understand factors like temperature stratification and airflow inside of a contained area. This understanding translates to process and equipment improvements that help protect product quality.
- Faster validation: By modeling the performance of HVAC installations and other utility systems, engineers can help accelerate the qualification and validation exercise, improving overall speed-to-market.
- A safer facility: Facility planners can use CFD to identify and closely control contamination risks, helping to protect both the product and the operators responsible for manufacturing it.
How we helped:
1. We confirmed the suitability of a CFD study.
For all of its advantages, CFD isn’t the perfect solution in every situation. Building and testing the appropriate computational environment takes time and financial investment. Since our team would need to visit the facility in order to measure its equipment and collect production data regardless of our approach, we advised this client not to pursue a CFD analysis right away. We would apply our expertise and unique perspective to see if we could make meaningful recommendations on-site, perhaps sparing our client from considerable expense while helping them achieve the desired result.
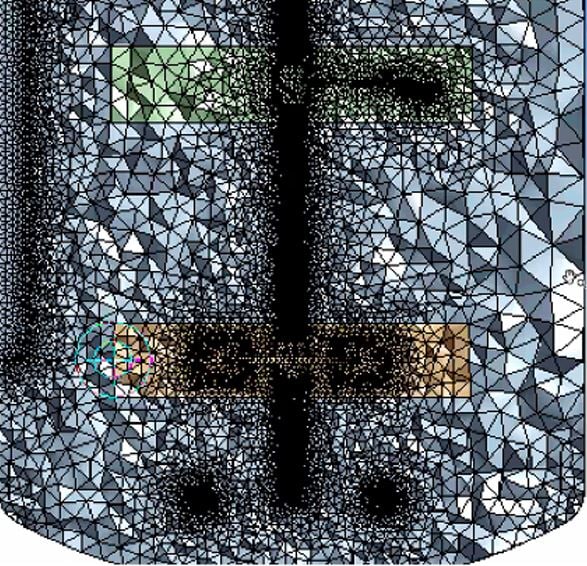
This is a close-up of a fermenter, rendered as a computer model for CFD analysis. In it, you can see how discrete cells form the computational domain. Smaller cells yield more detail during simulations, but take much longer to process.
2. We built and tested the computational area.
Following our team’s on-site examination, we concluded that the secret to improving what was already a considerably advanced and well-functioning system lay deep within the mechanics of the oven, securely enclosed and outside the reach of ordinary maintenance access. Only CFD analysis would pull back the curtain, helping us to identify those small but impactful opportunities for improved efficiency.
Before conducting our analysis, we needed to design the computational domain in which that analysis would take place. This was a lengthy process. The large-scale oven required a correspondingly large-scale model, which in turn needed to be broken into discrete cells. Together, these cells formed a polyhydron mesh; that mesh became our computational domain.
Once it was complete, we ran tests to observe the behavior of dynamic variables such as airflow inside the model. This satisfied us that the model could simulate fluid dynamics as expected, which meant we were ready to begin our CFD analysis.

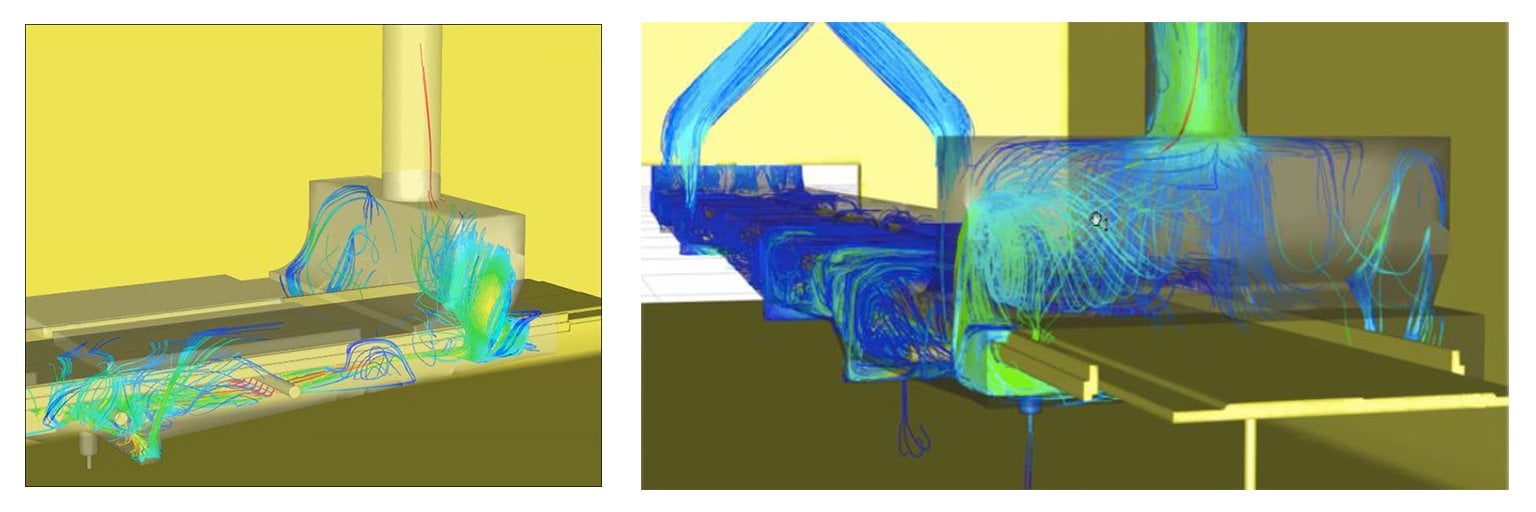
By simulating the temperature and velocity of airflow inside the oven, we confirmed that the model was behaving as expected.
3. We ran scenarios to help optimize the systems.
Once we built the computational domain and tested it for accuracy, we were ready to run simulations and look for opportunities to improve the oven’s efficiency.
Because this oven uses steam as its conductive force, you might assume that we would start by modeling steam flow. Given the complexity of the computational domain, though, steam flow simulations were incredibly intensive for the processor; each one took a week or more. The same was true with modeling the oven’s thermal dynamics. The more complexity we layered into our simulations, the more time we needed to reach our conclusions.
We hypothesized that we could find opportunities much more efficiently, and just as accurately, by modeling a simpler variable: airflow. Watching how air moves through the oven—what makes it accelerate, what makes it slow down, what determines its direction—could very well reveal if and how the client might improve their cooking time.
As we expected, our airflow analysis gave us valuable information.
Some of the oven’s steam pipes were located near exhaust fans, which helped to generate the turbulence necessary to conduct heated steam up towards the conveyor belt. Others were near open channels meant to drain condensation away from the conveyor belt. This too helped provide the necessary turbulence, but it meant that some steam was draining (or short-circuiting) away from the conveyor. A small tweak to the oven’s design would direct more steam towards meat moving along the conveyor belt, thereby improving cooking time.

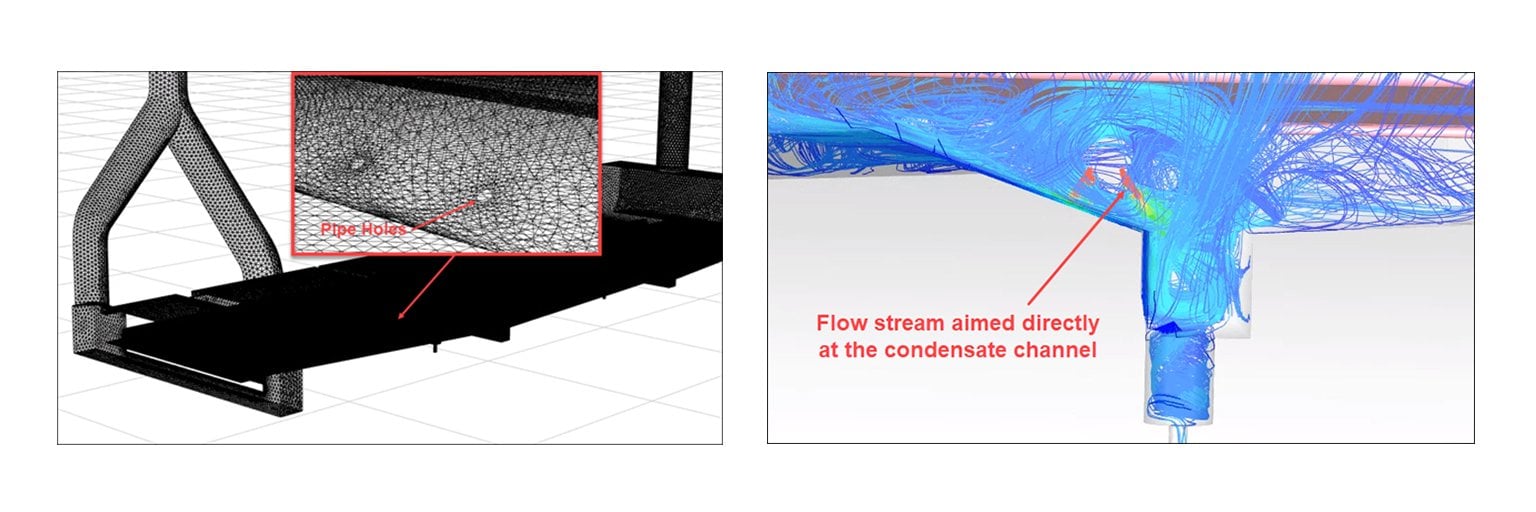
This simulated flow stream shows how steam was aimed directly at the condensate channel.
4. We recommended next steps to optimize the cooking system.
Now that our CFD analysis had successfully identified an opportunity for improved efficiencies, we shifted our attention to possible actions:
- Use baffles or fins at the base of the oven to induce turbulence and divert more steam towards the conveyor belt.
- Alternate the location of the steam tubes by moving some above the conveyor belt, helping to improve steam conduction down the length of the oven.
- Angle the steam tubes differently to help drive more heat towards the conveyor belt.
Which of these solutions will do the best job of improving cooking time? Here, too, CFD analysis holds the answer. Using our existing computational domain, we are now working with this client to run simulations and determine the best way forward.
Key Takeaways
Computational fluid dynamics may not be the right solution for your situation. Or it may be the only solution.
To know the difference, trust the experts at CRB. Using ANSYS® Fluent as our CFD tool, we help to answer complex questions and uncover hidden opportunities to optimize for clients in a wide variety of contexts.
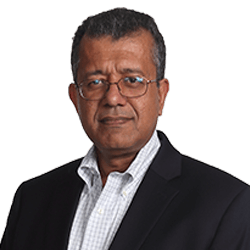
Riju Saini, PhD
Process Specialist
About the expert:
Riju, a Fellow of Simulation, Modeling, CFD, based in the Boston office, has extensive experience helping clients globally in the chemical, petrochemical, pharmaceutical, semi-conductor and allied industries. He drives CRB’s economic and technical due diligence services and works with clients worldwide to advance the state-of-the-art aspects of internal processes as well as those of simulation tools and process models.